Alex Colvin PhD ’99, Kenneth F. Kahn ’69 Dean of the ILR School, hosted “Supply Chain in Chaos” on April 14. Dean Colvin interviewed two manufacturing leaders with decades of experience working to source, produce, and deliver apparel to clients around the world.
Duncan Scott ’81, senior vice president of Strategic Sourcing and Quality for New Balance, and Anne Sutanto, vice CEO of PT. Pan Brother Tbk—the largest garment manufacturer in Indonesia—shared their insights on supply chain challenges and solutions.
Duncan noted that the current challenges began back in early 2020, with COVID-related lockdowns imposed in China. As COVID spread to pandemic proportions, nations around the world went into lockdown, causing a massive shutdown in retail operations. This resulted in a huge surge in online shopping and demand for products—creating what Duncan called a “whiplash effect” in the supply chain. The extreme downturn followed by a huge upturn “wreaked havoc” with the supply chain, he explained.
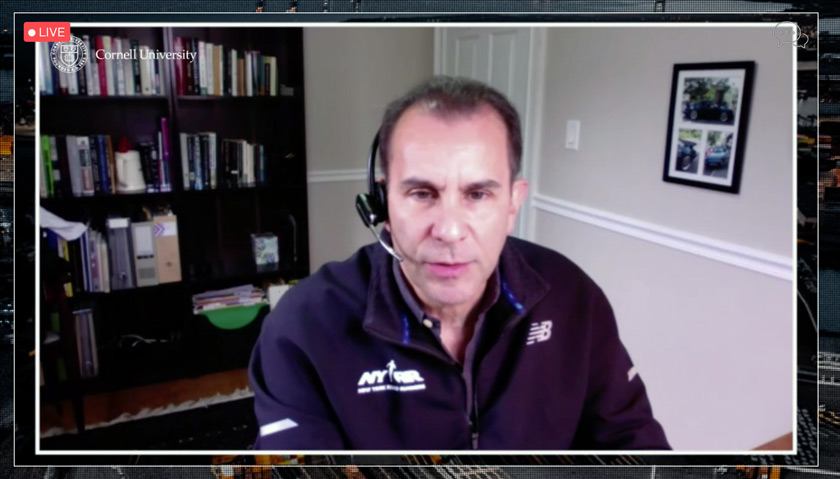
Shipping containers that cost $1.7K prior to the pandemic now cost $22K, and lead times to reserve container space have increased from a few days to several weeks. Duncan said that New Balance has responded by adjusting their calendars to account for shipping bottlenecks and by trying to increase efficiencies to offset shipping delays. Some of the strategies New Balance is using include:
- Reducing product development time
- Scaling up production in factories closer to the market
- Distributing production across multiple factories and locations, especially in countries with fewer pandemic related disruptions, like Indonesia
We need one another
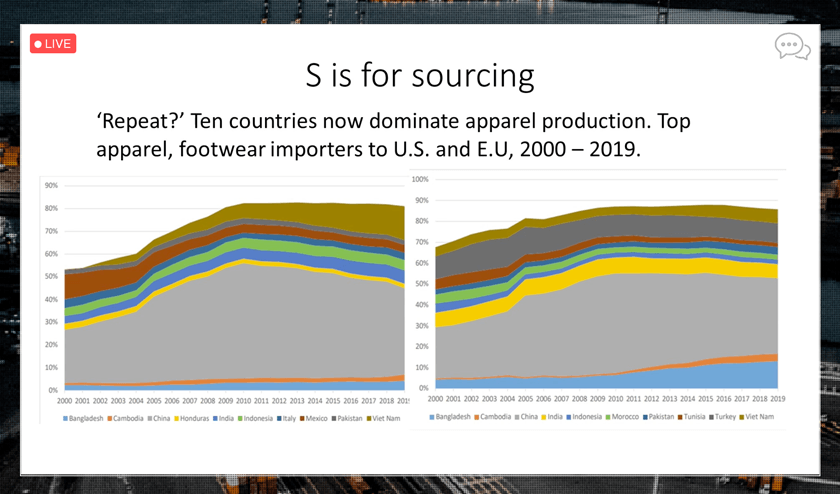
Dean Colvin noted that 80 percent of global apparel production is happening in just ten countries—meaning that suppliers and consumers are increasingly dependent on these countries for their clothing orders. Seven of these countries are located in Asia. To highlight how reliant U.S. consumers are on products sourced halfway around the world, he noted that 30,000 runners in the Boston Marathon on April 18 will compete wearing shoes made in factories located primarily in Asia.
Duncan explained that the process of shifting production to Asia has happened over many years. With growing consumer demand coming from China and India, he doesn’t foresee major shifts in production infrastructure back to the West. “There is a huge vortex of demand and supply in China,” he said, “and this will not change anytime soon.”
He noted that the era of low-cost labor has come to an end. “People have to be able to make decent wages. The only way to do this is by increasing efficiencies, so workers can make a living.”
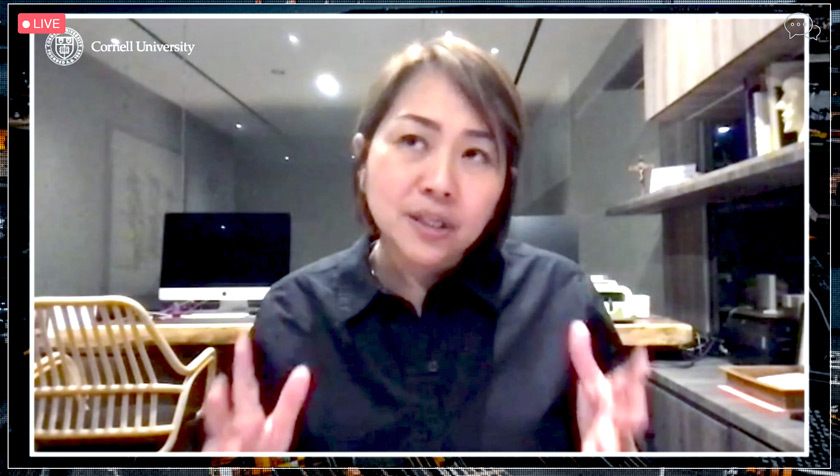
“It’s not about reducing the number of people,” Anne agreed. She explained that her company is working to reduce inefficiencies, rather than reducing their workforce. “We want to decrease the learning curve among our workers so that we can have Right-First-Time production and produce less waste,” she said, adding, “If we succeed, we can compensate for inflation.”
Anne noted that the Indonesian government has worked closely with the private sector throughout the pandemic to protect the health of factory workers, without closing down operations. She praised her government’s transparency in communicating COVID safety protocols, in purchasing a large supply of vaccines from multiple producers, and in promoting the efficacy of vaccines amongst the country’s population of 270M people. She said that 99 percent of her company’s 34,000 workers are vaccinated and boosted.
“We, as leaders, had to be there with our employees,” Anne said. “It’s not been easy, but with empathy, the proper controls, and constant communication among stakeholders, we were able to keep our workers and their families safe.”
Anne said her company, and all of us, collectively, have learned valuable lessons from the pandemic. “We need one another,” she said. “You can’t wear virtual clothes. You still need us to produce your clothes.”